Hosokawa Micron Powders GmbH fait partie depuis janvier 2020 du Réseau apprenant d’efficacité énergétique de la société RheinEnergie AG. Ce projet a pour but de continuer à abaisser durablement la consommation d’énergie et les rejets de CO2 des entreprises participantes – de 5 % par an au minimum. La première réunion de travail du LEEN Industrie a eu lieu le 6 février 2020 à la centrale thermique à turbines à gaz et à vapeur de Niehl 3, qui appartient à RheinEnergie AG.
Un réseau de transfert de savoir-faire dans le domaine de l’efficacité énergétique
Le LEEN est un Réseau apprenant d’efficacité énergétique, ce qui veut dire que plusieurs entreprises de différents secteurs se sont regroupées afin d’échanger sur le thème de l’efficacité énergétique. Les représentantes et représentants de ces entreprises partagent expériences et savoir-faire, étudient de nouveaux concepts et solutions et débattent sur des technologies, processus, méthodes et stratégies.
L’objectif consiste ici à maximiser le niveau de connaissances commun et à améliorer ainsi l’efficacité énergétique de l’ensemble des entreprises de l’alliance. En matière d’émissions de CO2 et de consommation d’énergie, on cible environ 5 % d’économies par an. Au-delà du transfert de connaissances proprement dit, cette démarche implique bien entendu des investissements importants qui seront toutefois amortis sur le long terme grâce aux économies d’énergie réalisées.
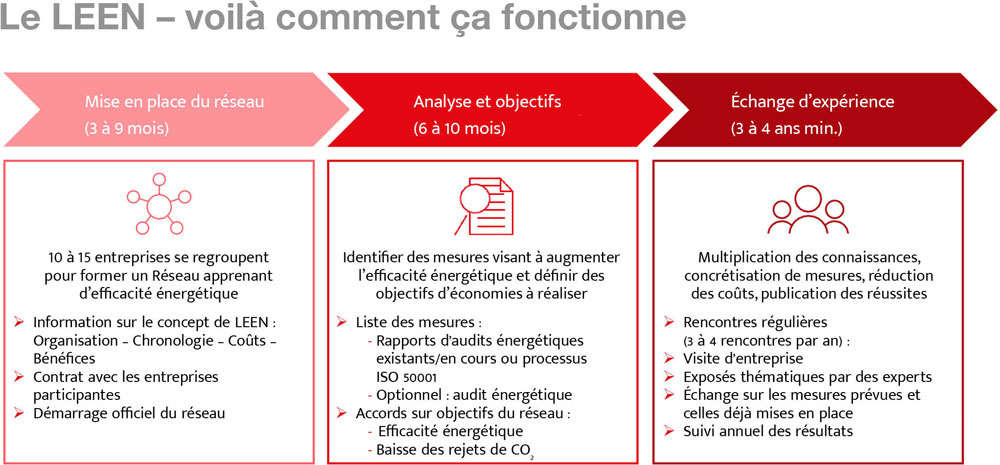
Schéma de fonctionnement d’un Réseau apprenant d’efficacité énergétique (graphique : RheinEnergie).
Il existe au total trois réseaux LEEN, qui sont issus des secteurs de l’industrie, du bâtiment et des hôpitaux. Hosokawa est l’une des 16 entreprises appartenant au réseau Industrie. Le projet est animé par les sociétés LEEN GmbH, RheinEnergie AG et l’Université technique de Cologne, laquelle fournit en outre une assistance scientifique. Les rencontres de réseau, qui ont lieu plusieurs fois par an, constituent l’un des fondements de cette coopération.
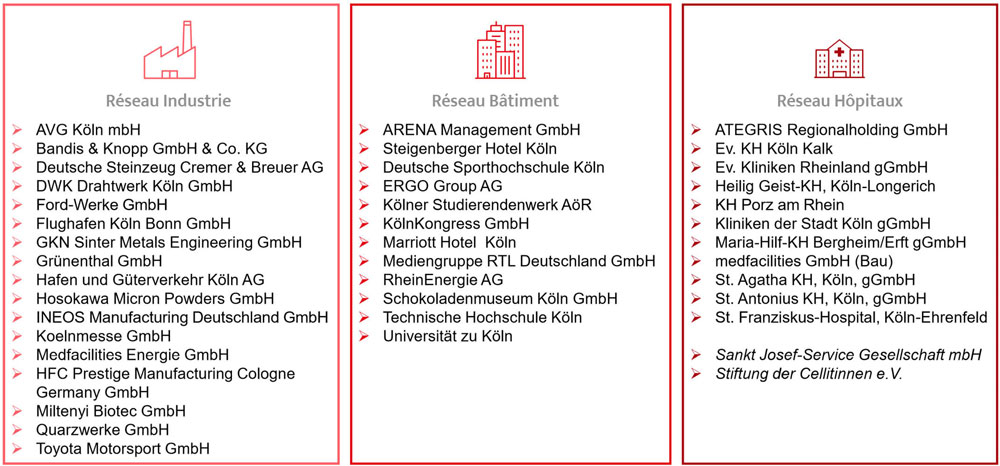
Voici les participants des réseaux d’efficacité énergétique de Cologne (graphique : RheinEnergie).
L’efficacité énergétique chez Hosokawa
Sur son site de Cologne, Hosokawa Micron Powders fabrique aujourd’hui en 3/8 et sur 18 unités de production plus de 14 000 tonnes par an des matériaux les plus divers destinés à près de 100 clients. L’objectif principal est le broyage ultrafin de matériaux chimiques et minéraux à des granulométries inférieures à 10 µm. Ce processus de broyage consomme beaucoup d’énergie. 13,5 % environ des coûts globaux sont des coûts énergétiques. Pour des raisons à la fois économiques et écologiques, il s’agit par conséquent ici d’identifier de nouveaux potentiels d’économie afin d’optimiser en permanence une efficacité énergétique qui atteint déjà à l’heure actuelle un niveau très élevé.
Comme l’explique Dr. Christoph Wadenpohl, directeur d’Hosokawa : « Eu égard au réchauffement climatique, les économies d’énergie réalisées grâce à l’optimisation continue des processus représentent bien davantage qu’une simple nécessité commerciale. Elles sont un impératif incontournable si nous voulons léguer aux générations futures un monde où il vaille la peine de vivre. Dans ce contexte, les échanges que nous avons avec des experts d’autres entreprises sont prometteurs en ce qu’ils génèrent de nouvelles impulsions et perspectives que nous accueillons très volontiers. Parce que le kilowattheure le plus efficace du point de vue énergétique, c’est celui que l’on ne consomme pas. »
Hosokawa est dès aujourd’hui certifié ISO 50001. D’importants investissements visant à accroître l’efficacité chez Hosokawa ont déjà été réalisés ou sont prévus. Ces mesures englobent notamment :
- Combinaison de 3 turbocompresseurs à vis à haut rendement et de turbocompresseurs, avec une puissance totale connectée de 1,5 MW pour la production annuelle de 31 M de m³ d’air comprimé.
- Récupération de chaleur intégrée dans les compresseurs à vis permettant de chauffer les halls de production et le bâtiment administratif
- Intégration d’un « Système de gestion de l’énergie globalement apprenant » (GLEM 4.0) pour le suivi en continu et la connexion à la télésurveillance
- Mise en œuvre d’une technologie d’installations sans huile pour le respect des critères de qualité les plus rigoureux
- Réalisation d’audits annuels pour l’optimisation permanente et l’identification de mesures visant à augmenter l’efficacité énergétique
- Extension progressive et réfection de la station d’air comprimé pour atteindre une puissance totale connectée de 2,3 MW
- Conversion en LED de l’éclairage des halls et mise en place de vitrages multiples.
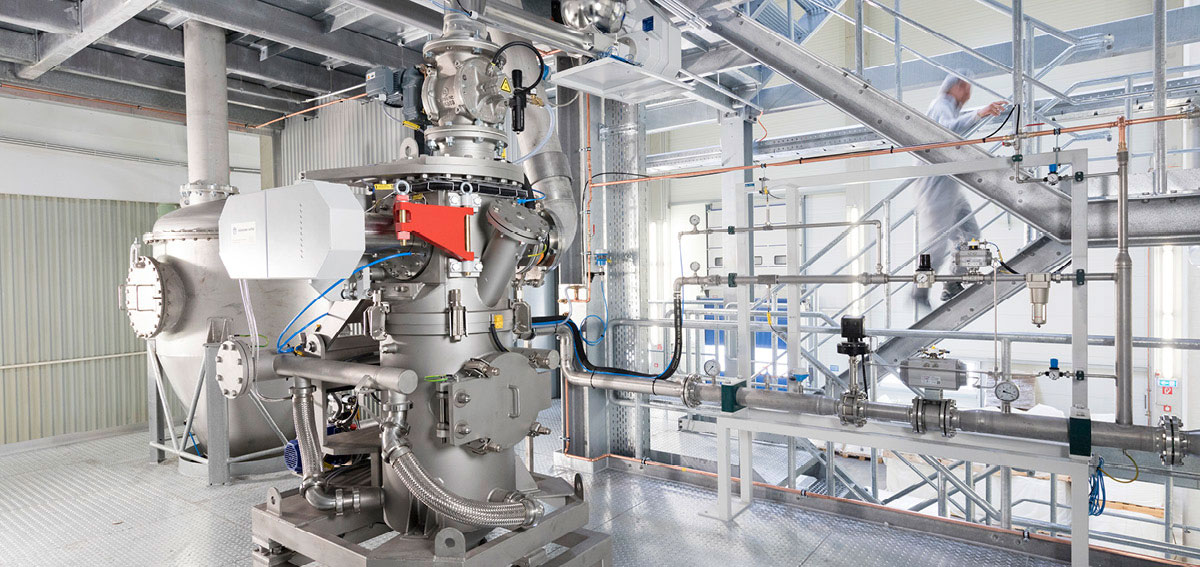
Broyeur à jet d’air chez Hosokawa (photo : Hosokawa).
Première réunion de travail du LEEN à la centrale thermique à haut rendement de Niehl 3.
C’est le 6 février dernier, sous le patronage du Pr Andreas Pinkwart, ministre de l’économie de Rhénanie-du-Nord-Westphalie, que s’est déroulée la première réunion de travail du LEEN Industrie à la centrale thermique à turbines à gaz et à vapeur de Niehl 3 de la société RheinEnergie AG.
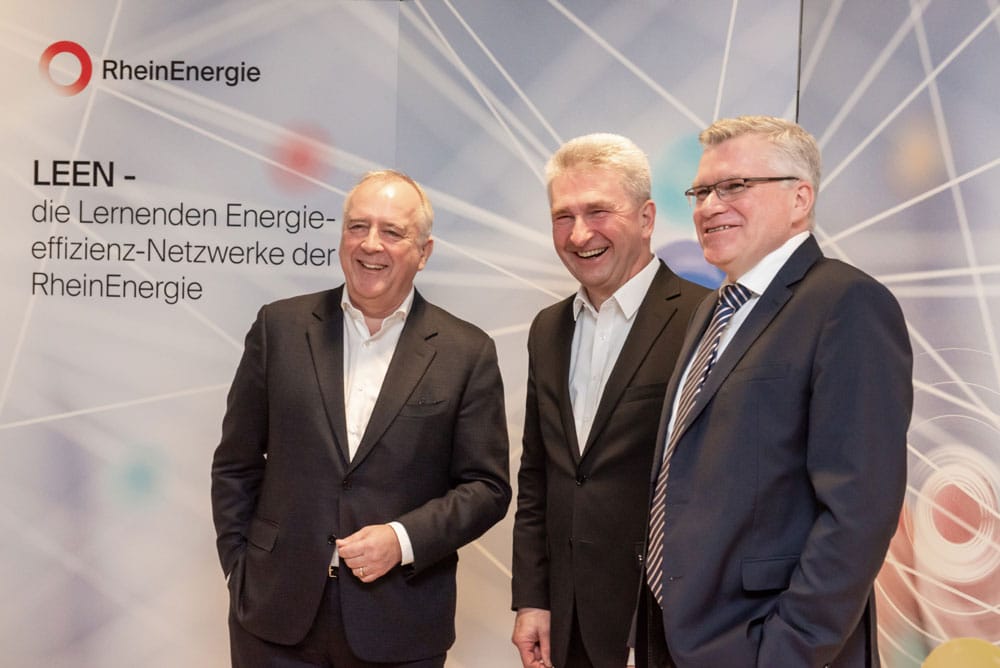
Gunnar Herrmann, président du directoire de Ford-Werke GmbH, Pr Andreas Pinkwart, ministre de l’Économie, de l’Innovation, de la Digitalisation et de l’Énergie, et Achim Südmeier, directeur général des ventes de RheinEnergie AG, début janvier, lors de la présentation des trois réseaux d’efficacité énergétique de Cologne (de g. à dr. ; photo : RheinEnergie).
Outre la présentation des participants et celle du concept de LEEN, une visite guidée de l’usine était également programmée. Ce site, qui avait été judicieusement choisi pour parler d’efficacité énergétique, offre de surcroît un exemple motivant : la centrale de Niehl 3 affiche un rendement de 88 %, ce qui en fait l’une des plus efficaces et les plus modernes au monde.
Dès cette première rencontre, les partenaires du réseau ont échangé activement sur leurs stratégies, actions et méthodes de travail, ainsi que sur les technologies et processus en usage dans le secteur de l’efficacité énergétique afin d’identifier de premières approches permettant d’accroître cette l’efficacité.
Emil Issagholian, de RheinEnergie, résume ainsi les résultats de cette réunion de lancement du projet : « Nous avons pu voir aujourd’hui que de nombreux responsables techniques et gestionnaires d’énergie sont confrontés à des challenges similaires. Sachant que tous les participants procèdent régulièrement à des audits énergétiques selon la norme DIN EN 16247 ou ont déjà mis en place un système de gestion de l’énergie selon la norme ISO 50001, l’identification et la mise en œuvre de mesures d’efficacité énergétique se retrouvent toujours au cœur des activités quotidiennes. Les exigences en constante évolution pour satisfaire aux normes, ainsi que la pression croissante pour réduire les émissions de CO2 placent les participants face à des défis accrus. Et c’est précisément par ces points critiques que nous voulons commencer dans le cadre du LEEN. »
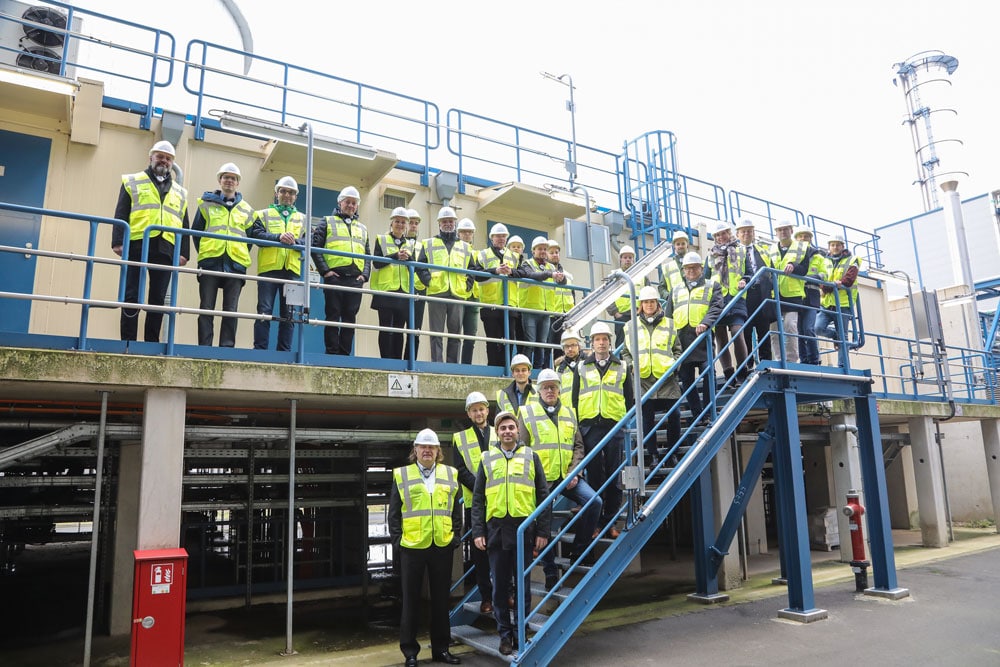
Des débuts réussis : la première rencontre de réseau du LEEN Industrie, qui a eu lieu à la centrale thermique à turbines à gaz et à vapeur de Niehl appartenant à la société RheinEnergie, a été l’occasion d’échanges intenses (photo : RheinEnergie).
La deuxième rencontre de réseau du LEEN Industrie aura lieu le 3 septembre prochain. Elle comprendra des visites des entreprises participantes ainsi que divers exposés thématiques. Figurent également à l’ordre du jour un échange en continu sur les mesures prévues et celles déjà appliquées, de même qu’un suivi des résultats.